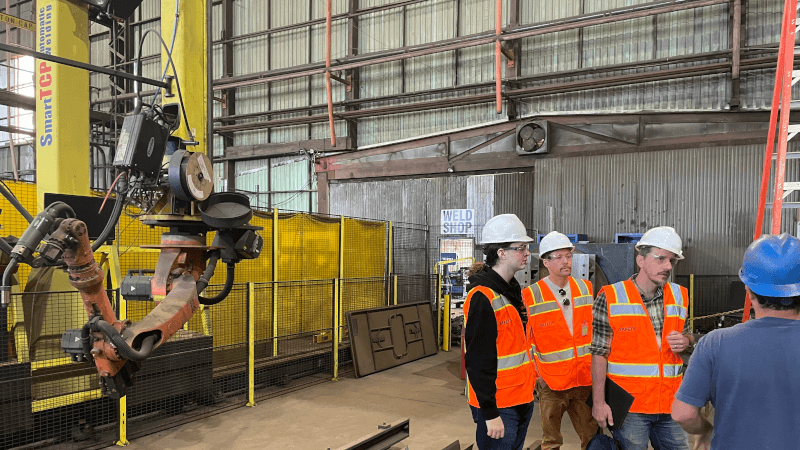
As a robotics integrator, we focus on using machine learning to enhance automation hardware. Our focus on sensor systems for capturing training data and neural networks for imitation learning allows us to enable robots to autonomously perform tasks that are difficult or impossible to automate with traditional methods. This approach is akin to how large language models operate, but instead of predicting the next token, we train robots to predict the next motion given what they see in front of them relative to the training data they have been provided.
In this quickly developing field, we have the option to utilize either traditional industrial robotics hardware from established partners like FANUC, Zebra, and Universal Robots or to explore new low-cost open-source models such as Stanford’s ALOHA Robot and the Annin Robotics AR4. Each type of hardware has its pros and cons, which we will explore in this article.
Industrial Robotics Hardware
Overview of Industrial Hardware Traditional industrial robots, such as those from FANUC, Zebra, and Universal Robots, have a long history of use in manufacturing and other industries. These robots are known for their precision, reliability, and ability to handle complex tasks in harsh environments.
Advantages of Industrial Hardware
- Reliability and Durability: Industrial robots have a proven track record of performance in demanding settings. They are built with hardened materials and can be made to withstand dust, dirt, and water, ensuring longevity and consistent operation in harsh environments.
- Support and Maintenance: Established manufacturers and their distribution networks can provide extensive support networks and comprehensive maintenance services, ensuring minimal downtime and quick resolution of issues.
- Compatibility and Integration: These robots integrate seamlessly with existing industrial systems, allowing for smooth transitions and upgrades within established workflows.
- Advanced Features: Industrial robots come equipped with sophisticated functionalities and precision capabilities, making them suitable for high-stakes applications that require accuracy and repeatability.
Disadvantages of Traditional Industrial Hardware
- Cost: The high upfront costs and ongoing maintenance expenses can be prohibitive for smaller businesses and startups and limit the possible applications with an acceptable return on investment.
- Complexity: Operating and maintaining these robots require specialized knowledge and training. Additionally, reliance on OEM parts can add to the complexity, cost and difficulty of repairs which can extend downtimes.
- Flexibility: Industrial robots typically run on closed-source proprietary software, often written in their own proprietary scripting language. Operators need to understand how to operate custom graphical user interface or write in custom scripting languages to program tasks, which can add raise barriers to utilizing multiple hardware vendors and add to vendor lock in. While many vendors do offer integrations with open source software like ROS2, their overall dependence on proprietary software can limit their exposure to rapid changes and new technologies happening in open-source communities.
New Low-Cost Open-Source Robotics Models
Overview of New Low-Cost Open-Source Models Emerging low-cost open-source models like Stanford’s ALOHA Robot and the Annin Robotics AR4 robot offer exciting new possibilities. ALOHA stands for A Low-cost Open-source Hardware System for Bimanual Teleoperation, developed and published by researchers at Stanford University. The ALOHA parts list and assembly tutorial is open source so you can build it yourself, or you can order a pre-built kit from our partner Trossen Robotics. These robots are relatively inexpensive ($30-40K), accessible, customizable, and designed to be built with readily available materials, including 3D-printed components.
Advantages of Low-Cost Open-Source Models
- Affordability: The lower upfront costs make these robots accessible to smaller businesses and startups, democratizing access to advanced robotics and opening up the field of possibilities for cost effective automation.
- Flexibility and Customizability: These robots offer a high degree of customization and adaptability to specific needs, with parts that are readily available and easy to replace or upgrade.
- Innovation and Community Support: The open-source community continuously drives improvements and innovations, fostering a collaborative environment for development.
- Ease of Learning and Use: These models are designed to be more accessible to those new to robotics and automation, lowering the barrier to entry for education and experimentation.
Disadvantages of Low-Cost Open-Source Models
- Reliability and Durability: These robots may not match the reliability and durability of established industrial hardware, especially in harsh or demanding environments. In order to be effective in industrial settings, they may need to be customized further adding to costs and timelines.
- Repeatability and Precision: The precision and repeatability of these models may not match that of traditional industrial robots, limiting their use in applications that require high levels of accuracy. However, this can be balanced by utilizing machine learning techniques shown in Standford’s ALOHA project to error correct on the fly in real time.
- Support and Maintenance: The support and maintenance infrastructure for open-source models is limited compared to traditional manufacturers, potentially leading to longer downtimes.
- Real-World Implementation Examples: With fewer real-world implementation examples, users may need to navigate challenges independently and innovate solutions without established guidelines.
Application of Machine Learning and Imitation Learning
Introduction to Imitation Learning Imitation learning involves training robots to perform tasks by mimicking human actions using transformer neural networks. This is similar to how large language models predict the next token in a sequence, but in this case predicting the next motion or action in a sequence. Transfering skills via machine learning offers significant advantages over traditional automation methods, which are far more rigid and prescriptive and require a technician to program specific routines and steps in a script.
The main hurtle to overcome for applying machine learning to robotics is the need for quality training data, which is not as readily available as language training data is on the internet. At RoZero Labs, we are developing systems for capturing training data from human demonstrations and using that data to train transformer neural networks for imitation learning.
Implementation in Traditional Hardware Traditional industrial robots can integrate computer vision and machine learning models to enhance their capabilities. For instance, FANUC robots have been used in recycling applications where computer vision and machine learning algorithms optimize the picking and placing of materials, improving efficiency and reducing errors.
FANUC Robot Demonstration
Implementation in Low-Cost Open-Source Models Open-source models benefit strongly from machine learning integration. The ALOHA Robot, for example, can be programmed with imitation learning algorithms to perform complex tasks in research and educational settings, showcasing the potential for low-cost, high-flexibility automation solutions. The fact that low cost hardware does not have the same repeatability and precision is balanced by the robots ability to error correct in real time.
ALOHA Robot Demonstration
ROS
What is ROS The Robot Operating System (ROS) is an open-source framework that provides the tools and libraries needed to develop robot applications. ROS is designed to support the integration of machine learning models, making it a valuable resource for both traditional and open-source robotics.
ROS in New Open-Source Robotics Hardware Open-source hardware often leverages ROS for developing and testing new applications. Its flexibility and comprehensive toolset make it ideal for experimental setups and rapid prototyping.
ROS in Traditional Hardware Most traditional industrial robotics manufacturers now offer some type of ROS integration. This compatibility allows for enhanced machine learning applications and easier integration of new technologies into existing systems.
Conclusion
Both traditional industrial automation hardware and new low-cost open-source robotics have their respective advantages and disadvantages. Traditional hardware offers reliability, durability, and advanced features, but at a higher cost and complexity. In contrast, open-source models provide affordability, flexibility, and a collaborative innovation environment, albeit with some trade-offs in reliability and support.
As the field of robotics continues to evolve, the choice between these options will depend on specific application needs, budget constraints, and the desired level of customization. Regardless of the choice, the integration of machine learning and imitation learning stands to significantly enhance the capabilities and potential of robotic automation.